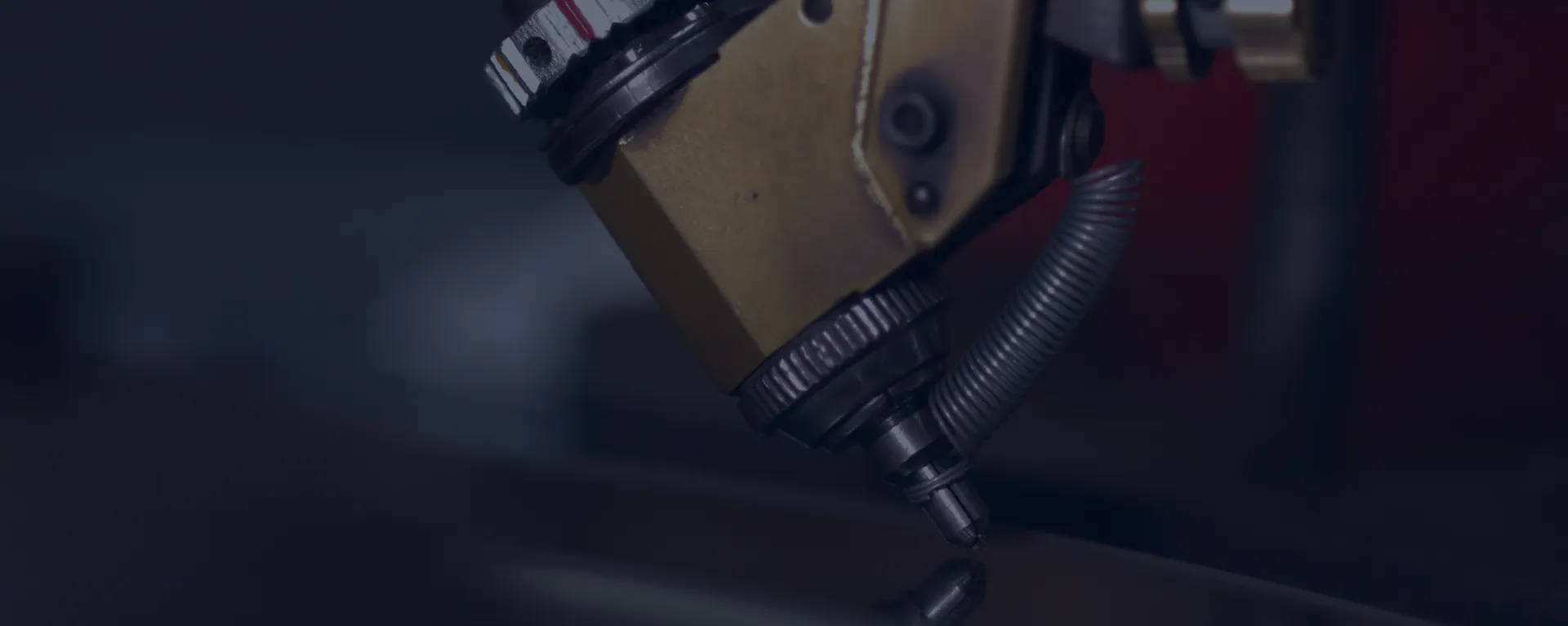
Where Science and Art Unite
Process: Where Science and Art Unite: Illuminating Discovery, Inspiring Creation.
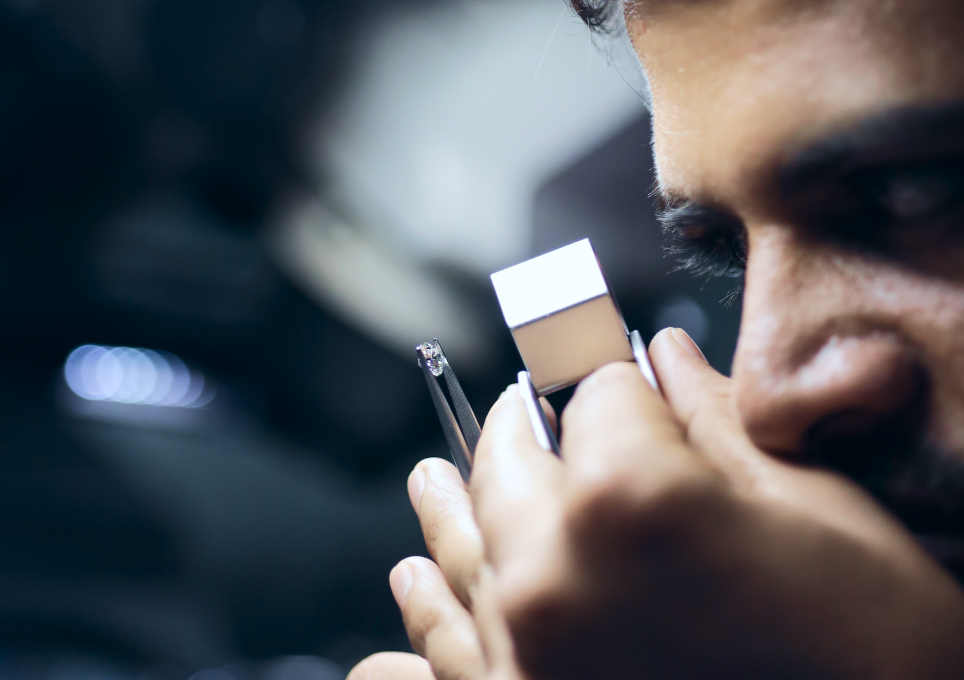
Welcome to the intersection of technology and creativity, where every diamond tells a story of mastery and elegance. Nestled in Surat, our state-of-the-art manufacturing facilities span over 2,34,594 sq. ft., housing cutting-edge machinery from industry leaders like Sarine. Manned by a workforce of over 8,000 highly skilled professionals, we boast a monthly production capability exceeding 225,000 carats of rough diamonds, empowering us to meet the demands of our clientele with unparalleled efficiency and quality.

Product Range
Products | Size | Colour | Clarity | Hue's |
---|---|---|---|---|
Non-Certified Goods | 0.9-5.5mm | D - M | IF-I3 | White, LB, LC |
Certified Goods - Rounds | 0.18ct-5ct | D - M | IF-I1 | White, LB, LC |
Certified Goods - Fancy | 0.50 Carat & above | D - M | IF-I1 | White, LB, LC |
The Touch of Perfection
Rough Sorting
The initial step in diamond cutting and polishing is analyzing the rough diamonds. Each rough diamond undergoes meticulous examination before cutting decisions are made. Diamonds are marked to maximize their value, considering imperfections and clarity. Sorting involves assessing potential yield based on cut, color, clarity, and carat size, categorizing them into thousands of polished diamond categories. Expertise is crucial in evaluating the rough diamond's appearance and optimizing its final value.
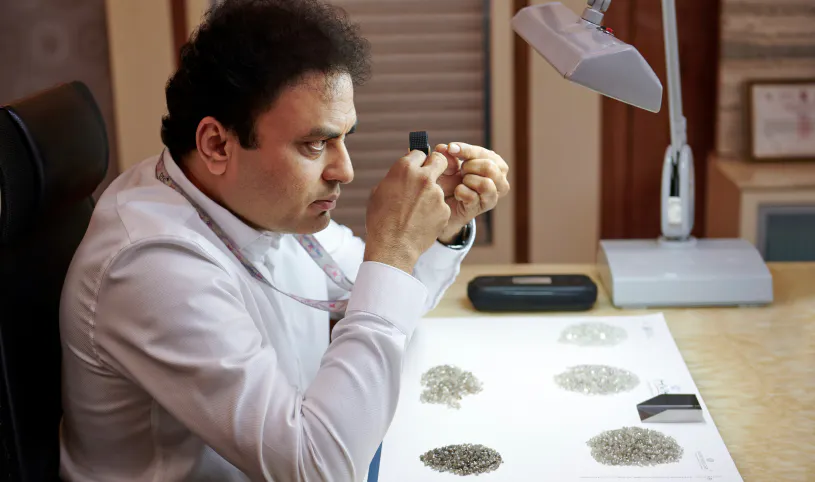
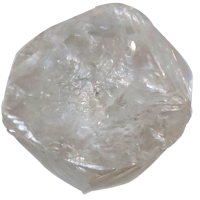
Scanning
The rough diamond is meticulously scanned from various angles using advanced imaging. Galaxy machines by Sarine Technologies help with the detection and mapping of internal features within the rough diamond. Additionally, scanning serves a vital role in quality control, enabling early detection of irregularities and defects, thus ensuring unparalleled accuracy and efficiency in maximising the diamond's value throughout the manufacturing process.
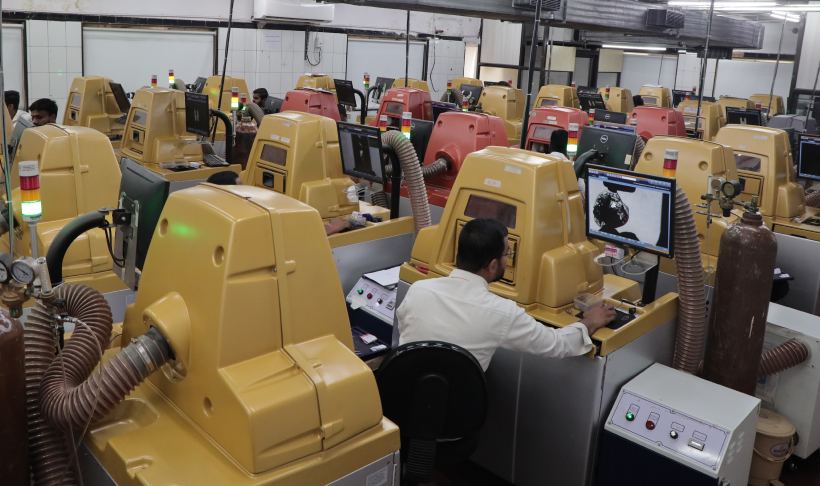
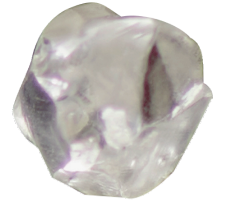
Planning
Planning is the process in which it is decided how the rough diamond will be cut and polished. Using Sarine software to analyze data from a Galaxy scan, Sarine's advanced algorithms help determine the ideal cut, facets, and dimensions to ensure the final polished gem reaches its full potential. Being able to extract the correct percentage of yield is extremely important at this stage.
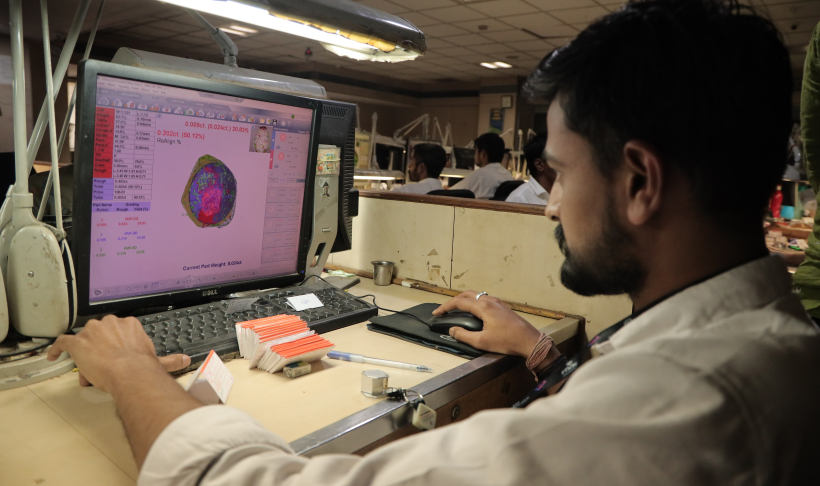
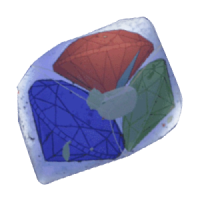
Laser Marking
The laser marking stage in diamond manufacturing, following planning and preceding sawing, employs advanced 3D laser technology to precisely mark the rough diamond for cutting. This process integrates specialized software to analyze the diamond's structure, map inclusions, and determine optimal cutting paths, ensuring minimal weight loss and maximizing clarity and value. Experienced markers finalize the design, using automated laser marking to guide the cuts accurately. This crucial step enhances precision, reduces waste, and ensures the highest quality and value in the final gem.
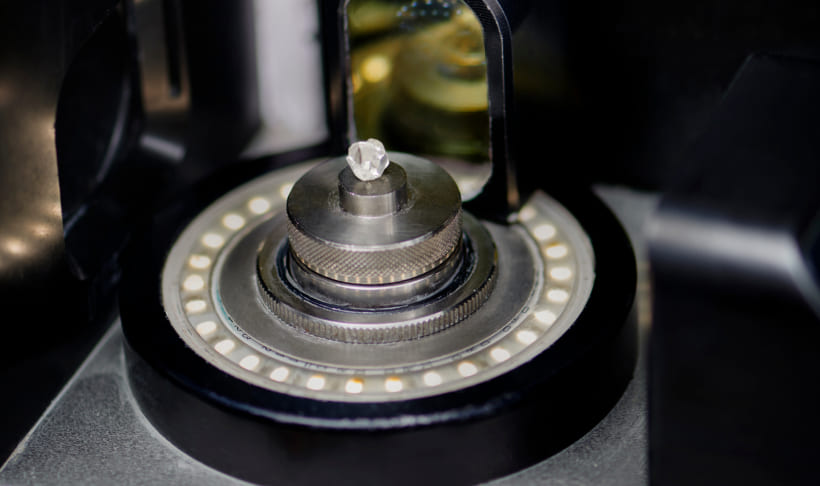
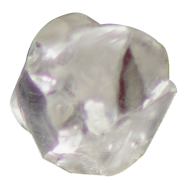
Laser Sawing
With the plan in place, the rough diamond is precisely cut into smaller pieces using the Quazer™, an advanced high-quality, green laser diamond sawing and shaping system. Guided by the software's instructions, the Quazer™ ensures clean and accurate cuts, preparing the diamond for the next stage with high productivity, and flexibility in cutting profiles while minimizing the risk of breakage.
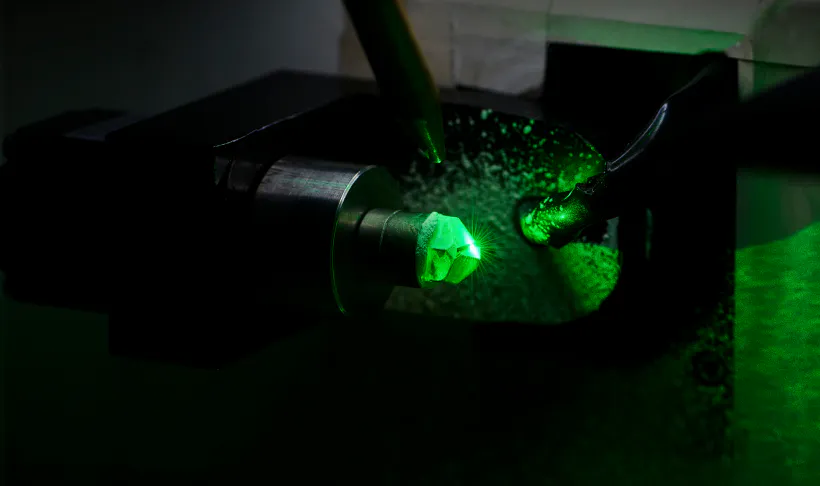
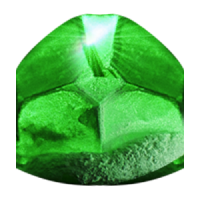
Bruting
Bruting is a critical step in diamond cutting, particularly for round brilliants. In this process, diamonds are rounded using a diamond disc coated with diamond powder, this gradually shapes the diamond into a round form, refining its girdle and ensuring symmetry. This step is essential for achieving the desired shape and proportions in a round brilliant diamond, ultimately enhancing its brilliance and value.
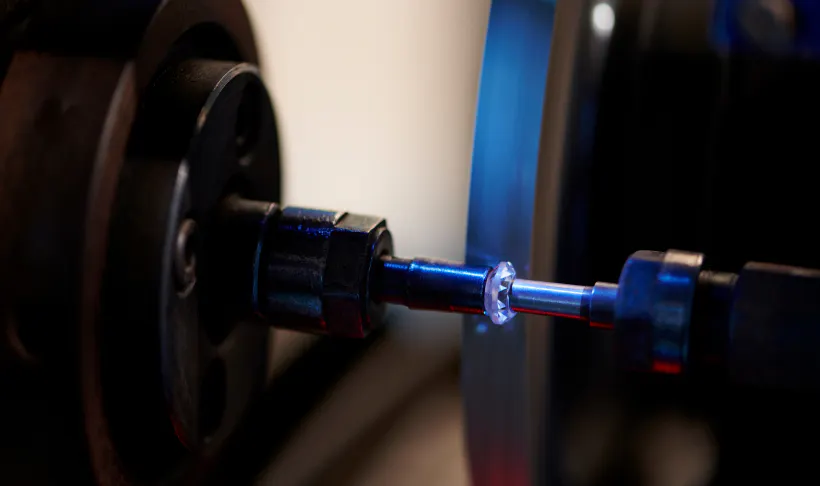
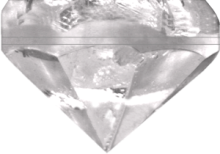
Faceting and Polishing
After bruting, the diamond undergoes faceting and polishing, where skilled artisans steadily and meticulously craft its facets to maximize brilliance and fire, unveiling its inner beauty. Following this, during blocking, essential features like pavilion mains, crowns, culet, and table facet are added, shaping the diamond's foundation. Finally, brillianteering further refines the gem, enhancing its sparkle and allure, culminating in a radiant masterpiece ready to adorn exquisite jewelry, captivating hearts with its brilliance.
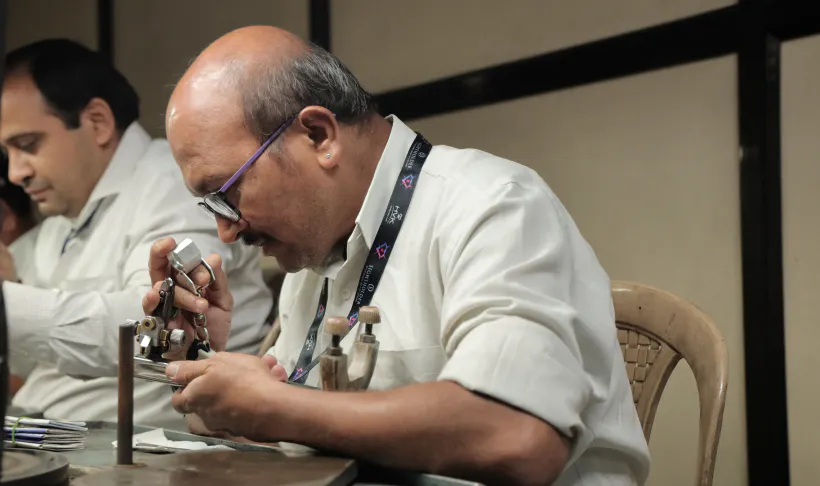
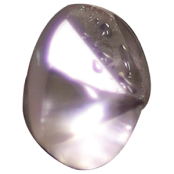
Quality Check
We ensure that every single diamond crafted at HVK International is an “HVK” diamond. Quality assurance checks at each stage ensure alignment with plans and flexibility to address market changes or optimise yield if needed. At HVK International, every diamond undergoes a rigorous "HVK" diamond process, including a comprehensive 360-degree mathematical scan for symmetry and cut, ensuring perfection from every angle. Authenticity is guaranteed with scans under diamond testers.
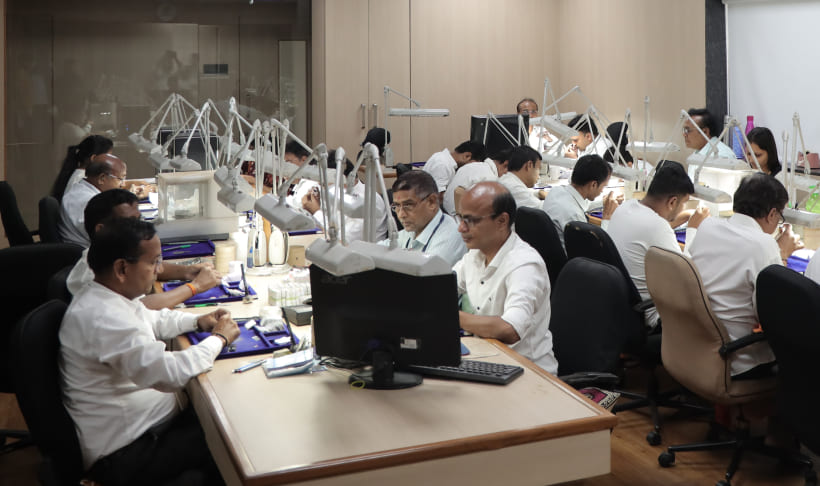
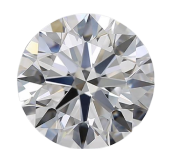
Grading and Assorting
Finally, diamonds are meticulously graded and assorted based on their unique characteristics, ensuring they meet HVK International's exacting standards for quality and value. This ensures that each diamond is carefully classified and prepared to meet the diverse needs and preferences of our clientele, guaranteeing satisfaction and confidence in every purchase.
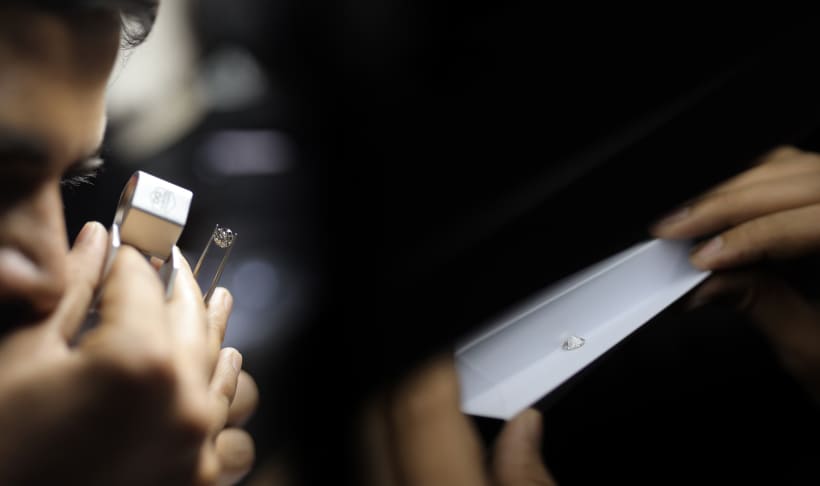
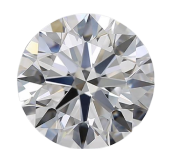